The precision manufacturing landscape has undergone a transformative evolution with the advent of 5-axis laser machining technology, enabling unprecedented accuracy and efficiency in processing complex geometries across diverse industrial applications. This advanced manufacturing approach combines sophisticated laser systems with multi-axis positioning capabilities, delivering exceptional results in automotive tooling, 3C electronics, medical devices, and aerospace components. OPMT Laser’s comprehensive portfolio of 5-axis laser machining centers represents the cutting edge of this technological revolution, offering manufacturers the precision and flexibility required for next-generation production demands.
Modern 5-axis laser processing systems achieve positioning accuracies of ±0.005mm while maintaining rapid traverse speeds up to 30 m/min, significantly outperforming traditional machining methods in terms of both precision and productivity. The integration of advanced laser galvanometer technology with sophisticated multi-axis control systems enables manufacturers to process ultra-hard materials including PCD, CBN, ceramics, and advanced composites with exceptional surface quality and dimensional accuracy.
Understanding 5-Axis Laser Machining Fundamentals
Core System Architecture
5-axis laser machining systems incorporate three linear axes (X, Y, Z) and two rotational axes (typically B and C), providing complete geometric freedom for complex part processing. This configuration enables simultaneous movement across all five axes, allowing the laser beam to maintain optimal angle and focus throughout the machining process regardless of workpiece complexity.
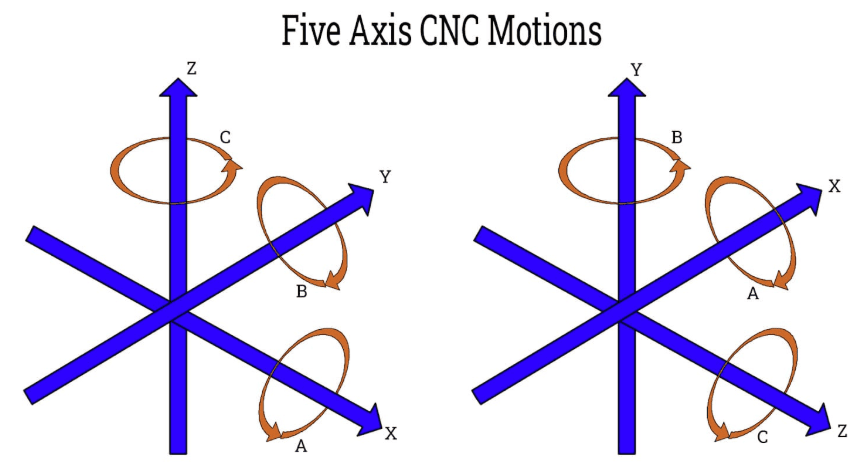
The fundamental advantage of 5-axis geometry lies in its ability to eliminate multiple setups and reduce accumulated tolerance errors. Unlike traditional 3-axis systems that require workpiece repositioning for complex geometries, 5-axis machines complete intricate parts in a single clamping operation, ensuring superior accuracy and significantly reduced cycle times.
Key Performance Parameters:
- Linear positioning accuracy: ±0.005mm across X, Y, Z axes
- Rotational positioning accuracy: ±10 arcseconds for B and C axes
- Repeatability: ±0.003mm for linear movements, ±5 arcseconds for rotational
- Maximum tool diameter capacity: Up to 200mm depending on configuration
- Workpiece weight capacity: 25-300kg depending on system specification
Advanced Motion Control Integration
Modern 5-axis laser systems employ linear motor drives for all linear axes, providing exceptional dynamic response without mechanical backlash. The rotational axes utilize high-precision torque motors with direct drive configurations, ensuring smooth motion throughout the full range of angular movement. All axes implement full closed-loop grating scale feedback systems, delivering the precision required for demanding manufacturing applications.
The integration of sophisticated NUM CNC control systems provides comprehensive motion coordination with advanced features including RTCP (Rotation Tool Center Point) functionality. This capability ensures that the laser focal point remains precisely positioned during simultaneous multi-axis movements, critical for maintaining consistent processing quality across complex three-dimensional geometries.
Technical Advantages Over Conventional Methods
Precision and Accuracy Comparison
5-axis laser machining demonstrates significant advantages over traditional processing methods, particularly in applications requiring complex geometries and ultra-hard material processing. The elimination of mechanical tool wear inherent in laser processing ensures consistent dimensional accuracy throughout production runs.
Processing Method | Positioning Accuracy | Surface Roughness | Processing Speed | Tool Wear |
---|---|---|---|---|
5-Axis Laser | ±0.005mm | Ra 0.1-0.3μm | 3x faster | None |
Traditional EDM | ±0.010mm | Ra 0.3-0.8μm | Baseline | High electrode consumption |
Grinding | ±0.008mm | Ra 0.2-0.5μm | 2x slower | Wheel wear/dressing required |
Mechanical Milling | ±0.015mm | Ra 0.4-1.2μm | Variable | Tool replacement frequent |
Economic Impact Analysis
The implementation of 5-axis laser machining technology delivers measurable economic benefits through multiple operational improvements. Processing time reductions of 200-300% compared to conventional EDM methods result in significant productivity gains, while the elimination of consumable electrodes and cutting tools reduces ongoing operational costs by approximately 50%.
Energy efficiency represents another crucial advantage, with femtosecond laser systems consuming 44% less energy than traditional thermal processing methods while eliminating chemical waste streams entirely. This environmental benefit aligns with modern sustainability requirements while reducing regulatory compliance costs.
Laser Galvanometer Integration and Performance
Precision Beam Positioning Systems
The heart of advanced 5-axis laser machining lies in sophisticated galvanometer scanning systems that provide rapid, precise beam positioning capabilities. These electro-optical devices utilize high-speed mirrors to direct laser beams with positioning accuracies reaching ±1-2 microradians, enabling intricate pattern generation and complex contour processing.
OPMT’s advanced galvanometer systems operate at scanning frequencies exceeding 1,000 Hz while maintaining positioning stability within ±0.1 microradians per degree Celsius temperature variation. This thermal stability ensures consistent processing quality throughout extended production runs, critical for high-volume manufacturing applications.
Galvanometer System Specifications:
- Scanning frequency range: 100-2,000 Hz sustained operation
- Angular positioning accuracy: ±1-2 microradians across operational range
- Thermal drift coefficient: 1.67 across all critical dimensions.
Medical Device Manufacturing
Medical device applications demand the highest levels of precision and surface quality, making 5-axis laser machining an ideal processing solution. FDA-compliant processing protocols ensure complete traceability and validation documentation required for medical device manufacturing regulations.
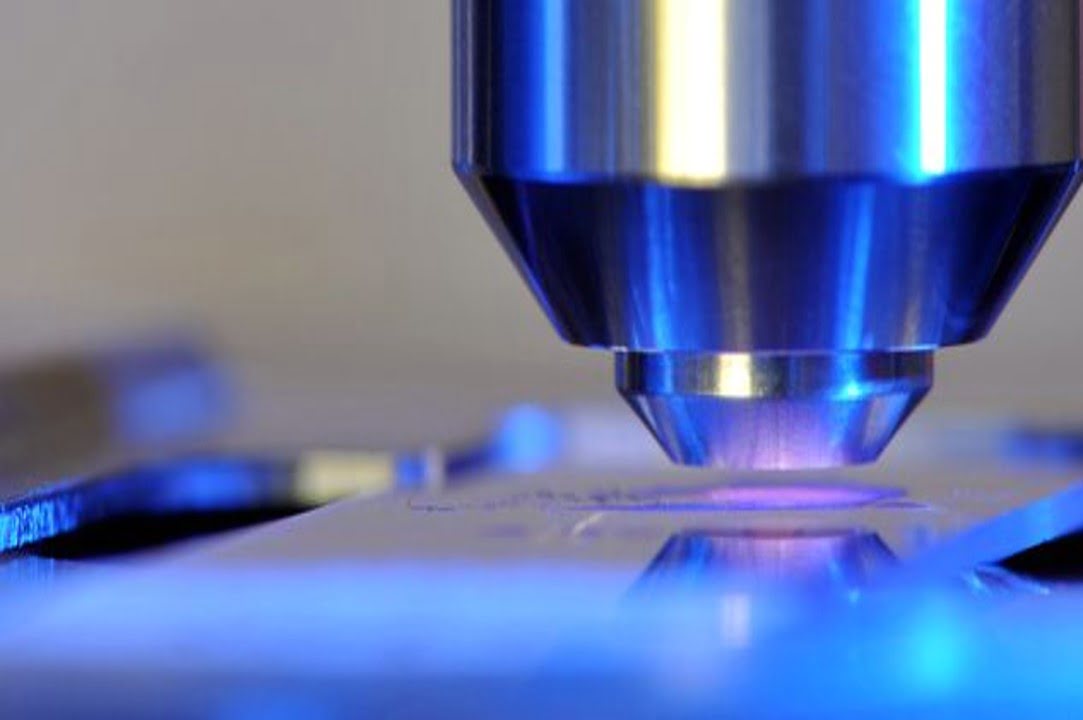
Critical medical device applications include:
- Cardiovascular stent processing: Sub-5μm feature creation with controlled heat-affected zones
- Surgical instrument manufacturing: Complex geometry processing with mirror-finish requirements
- Implantable device surface modification: Biocompatible surface texturing for improved integration
- Microfluidic device fabrication: Precision channel creation in various substrate materials
The Micro3D L530V femtosecond system specifically addresses medical device requirements with pulse widths ≤400fs and repetition frequencies ≥1MHz, enabling “cold processing” that eliminates thermal damage in sensitive materials.
3C Electronics Manufacturing
The rapid evolution of consumer electronics drives demand for increasingly precise manufacturing capabilities. 3C electronics applications require sub-micron accuracy for component processing, circuit board via drilling, and precision marking operations.
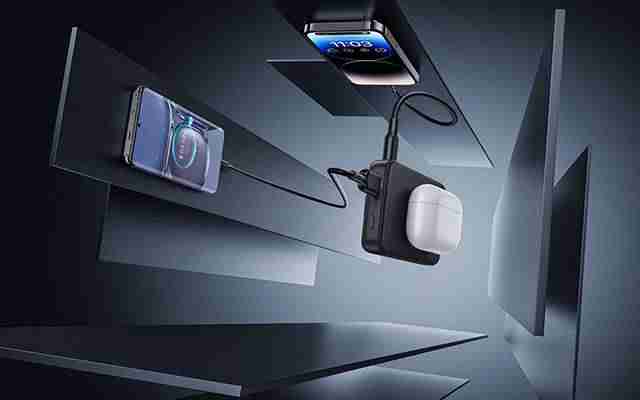
Key 3C Applications:
- Smartphone component processing: Camera module assembly and connector manufacturing
- Circuit board via drilling: High-speed precision hole drilling with minimal heat-affected zones
- Component marking and identification: Permanent traceability marking without material damage
- Flexible circuit processing: Precise cutting and via creation in polyimide substrates
Performance data from 3C manufacturing implementations show 65% reduction in positioning-related defects and achievement of 99.97% process yield through optimized laser processing parameters.
OPMT Product Line Technical Specifications
Comprehensive System Comparison
OPMT Laser’s portfolio encompasses multiple 5-axis configurations optimized for specific application requirements. The following comparison highlights key specifications across the product range:
Model | Travel Range (X/Y/Z) | Positioning Accuracy | Laser Power | Max Workpiece | Typical Applications |
---|---|---|---|---|---|
Light 5X-40V | 400/250/300mm | ±0.005mm | 100W | φ200 x 200mm | 3C electronics, PCD tools |
Light 5X-60V | 600/250/300mm | ±0.005mm | 100W | φ350 x 200mm | Automotive tooling, aerospace |
LP550V | 520/640/480mm | ±0.008mm | Variable | φ400 x 310mm | Rotary cutting, compound processing |
Micro3D L530V | Custom configuration | ±0.010μm | 40W femtosecond | Variable | Ultra-precision, medical devices |
Advanced Feature Integration
All OPMT 5-axis systems incorporate modular design architecture enabling function expansion and software upgrades throughout the equipment lifecycle. The direct drive indexing structure ensures high angular accuracy and excellent dynamic response characteristics across all rotational axes.
Standard Equipment Features:
- Natural marble machine beds: Superior thermal stability and vibration damping
- Linear motor drives: Zero backlash, high dynamic response for all linear axes
- High-precision torque motors: Direct drive rotational axes with exceptional accuracy
- Full closed-loop control: Grating scale feedback on all axes for maximum precision
- Modular optical systems: CCD positioning cameras and high-precision probes included
Implementation Guidelines and Best Practices
System Installation and Setup
Successful 5-axis laser machining implementation requires careful attention to environmental conditions and installation procedures. Optimal performance demands controlled temperature environments (±2°C variation), adequate power supply infrastructure, and proper vibration isolation.
Installation Requirements:
- Environmental Control: Temperature stability ±2°C, humidity control 45-65% RH
- Power Infrastructure: Stable 380V ±10% three-phase supply with appropriate capacity
- Compressed Air: 0.7 MPa supply pressure with 500 L/min flow rate minimum
- Floor Space: Adequate clearance for machine envelope plus maintenance access
- Vibration Isolation: Proper foundation design to minimize external vibration transmission
Process Optimization Strategies
Achieving optimal results requires systematic approach to process parameter development and validation. Material-specific processing parameters must be established through controlled testing protocols, with documentation maintained for regulatory compliance requirements.
Optimization Methodology:
- Material Characterization: Comprehensive analysis of thermal and optical properties
- Parameter Development: Systematic testing of laser power, pulse duration, and scanning speeds
- Quality Validation: Statistical process control implementation with capability studies
- Process Documentation: Complete parameter sets with validation data for regulatory compliance
- Continuous Improvement: Ongoing optimization based on production feedback and quality metrics
Maintenance and Quality Assurance
Preventive maintenance protocols ensure consistent long-term performance and maximize equipment uptime. Predictive maintenance strategies utilizing comprehensive system diagnostics enable optimization of maintenance schedules while minimizing unplanned downtime.
Maintenance Schedule Framework:
- Daily Procedures: System diagnostic review, optical component inspection, coolant level verification
- Weekly Protocols: Comprehensive calibration verification, mechanical inspection, software backup procedures
- Monthly Validation: Full system calibration using traceable standards, complete documentation updates
- Quarterly Assessment: Comprehensive performance analysis, preventive component replacement, upgrade evaluation
Future Technology Trends and Developments
Artificial Intelligence Integration
The next generation of 5-axis laser machining systems will incorporate machine learning algorithms for real-time process optimization and predictive quality control. AI-enhanced systems will automatically adjust processing parameters based on material variations, environmental conditions, and quality feedback, ensuring optimal results with minimal operator intervention.
Emerging AI Applications:
- Adaptive process control: Real-time parameter optimization based on quality feedback
- Predictive maintenance: Advanced analytics for component failure prediction and optimization
- Quality assurance: Automated defect detection and process correction capabilities
- Production optimization: Intelligent scheduling and workflow management integration
Industry 4.0 Integration
Advanced connectivity and data analytics capabilities enable seamless integration with digital manufacturing ecosystems. IoT-enabled systems provide comprehensive operational data for continuous improvement initiatives while supporting remote monitoring and diagnostic capabilities.
The evolution toward digital twin technology will enable virtual system modeling for process optimization and training applications. This approach provides continuous performance enhancement opportunities while reducing implementation risks for new applications.
Conclusion and Technology Recommendations
5-axis laser machining technology represents a transformative advancement in precision manufacturing, offering unprecedented capabilities for complex geometry processing across diverse industrial applications. The combination of advanced laser systems, sophisticated motion control, and comprehensive automation delivers measurable improvements in productivity, quality, and operational efficiency.
OPMT Laser’s comprehensive portfolio provides optimized solutions for specific application requirements, from high-volume 3C electronics manufacturing to precision medical device production. The integration of advanced laser galvanometer systems with sophisticated 5-axis positioning capabilities enables manufacturers to achieve previously unattainable levels of precision and efficiency.
Disclaimer
This content is compiled by OPMT Laser based on publicly available information for reference only; mentions of third-party brands and products are for objective comparison and do not imply any commercial association or endorsement.