Understanding material selection for laser processing applications requires comprehensive analysis of thermal, optical, and mechanical properties that directly influence processing outcomes and component quality. This technical analysis examines the fundamental differences between Nylon 12 (PA12) and Polypropylene (PP) for industrial laser manufacturing, providing engineers with evidence-based insights for optimal material selection and process optimization strategies.
The selection between PA12 and PP involves critical considerations including thermal characteristics, moisture absorption properties, and laser processing compatibility. These materials serve different roles across automotive, electronics, and medical device manufacturing sectors, each offering distinct advantages depending on specific application requirements and processing conditions.
Material Properties Foundation: Technical Characteristics
Thermal Performance Analysis
Based on established material property databases and industry standards, PA12 and PP demonstrate significantly different thermal behaviors that directly impact laser processing parameters and quality outcomes.
Nylon 12 (PA12) Thermal Profile:
- Heat Deflection Temperature: 175°C (347°F) per ISO standards
- Melting Temperature Range: Typically 178-184°C
- Thermal Stability: Maintains structural integrity at elevated temperatures up to 185°C
- Moisture Absorption: 0.3-7% water absorption by weight
Polypropylene (PP) Thermal Profile:
- Heat Resistance: Limited to temperatures below 180°F
- Melting Temperature Range: Generally 160-168°C
- Moisture Absorption: Exceptional resistance with only 0.01% water absorption
- Chemical Stability: Superior resistance to moisture and chemical exposure
The fundamental difference in moisture absorption represents a critical factor for laser processing applications. PA12’s higher moisture absorption can impact dimensional stability in humid environments, while PP maintains consistent properties across varying environmental conditions.
Laser Processing Compatibility Assessment
Material Suitability for Laser Applications
According to OPMT’s materials compatibility guide, both PA12 and PP are suitable for laser processing applications, though each material requires specific parameter optimization for optimal results.
Polypropylene (PP) Processing Characteristics:
- Requires careful handling during laser processing due to thermal sensitivity
- Best practices involve adjusting laser parameters according to material thickness
- Variability in thickness can significantly impact processing consistency
- Chemical resistance properties make it valuable for specific industrial applications
Nylon 12 (PA12) Processing Advantages:
- Recognized for exceptional strength and lightweight properties
- Widely utilized in automotive components and 3D printing applications
- Demonstrates strong chemical resistance to oils and solvents
- Maintains dimensional stability under processing conditions
Processing Parameter Considerations
OPMT’s processing guidelines emphasize the importance of material-specific parameter optimization. For PP applications, precision laser cutting technology requires careful power density control and thermal management to prevent material distortion.
Industry Applications and Manufacturing Solutions
Automotive Industry Applications
The automotive sector utilizes both materials for different applications based on their specific properties and processing characteristics.
PA12 Automotive Applications:
- Engine component manufacturing requiring high impact strength
- Gears and bearings for critical automotive systems
- Functional prototypes in additive manufacturing processes
- Components requiring chemical resistance to automotive fluids
PP Automotive Applications:
- Battery casings where chemical resistance is critical
- Large components where cost optimization is primary concern
- Applications requiring excellent moisture resistance properties
Electronics and 3C Industry Solutions
3C electronic digital industry solutions benefit from both materials depending on specific requirements. The electronics sector particularly values PA12 for applications requiring dimensional stability and mechanical strength, while PP serves applications where moisture resistance and cost effectiveness are prioritized.
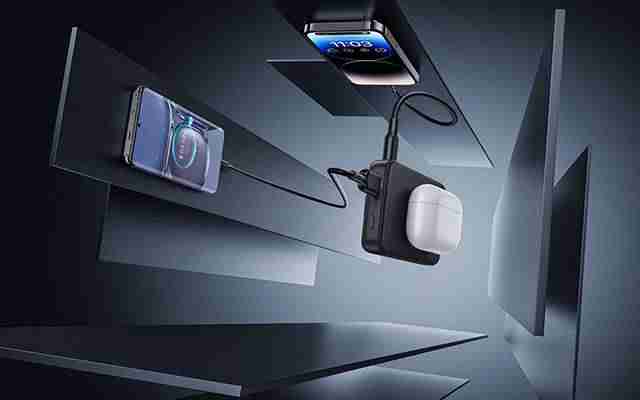
Key Electronics Applications:
- Smartphone and electronic device components
- Protective housings requiring chemical resistance
- Lightweight structural elements for portable devices
- Components requiring long-term dimensional stability
Technical Processing Considerations
OPMT Laser Processing Systems
OPMT’s advanced laser processing systems are specifically designed to handle diverse materials including PA12 and PP. The Light 5X Series laser machining centers provide the precision and control necessary for optimal processing of both materials.
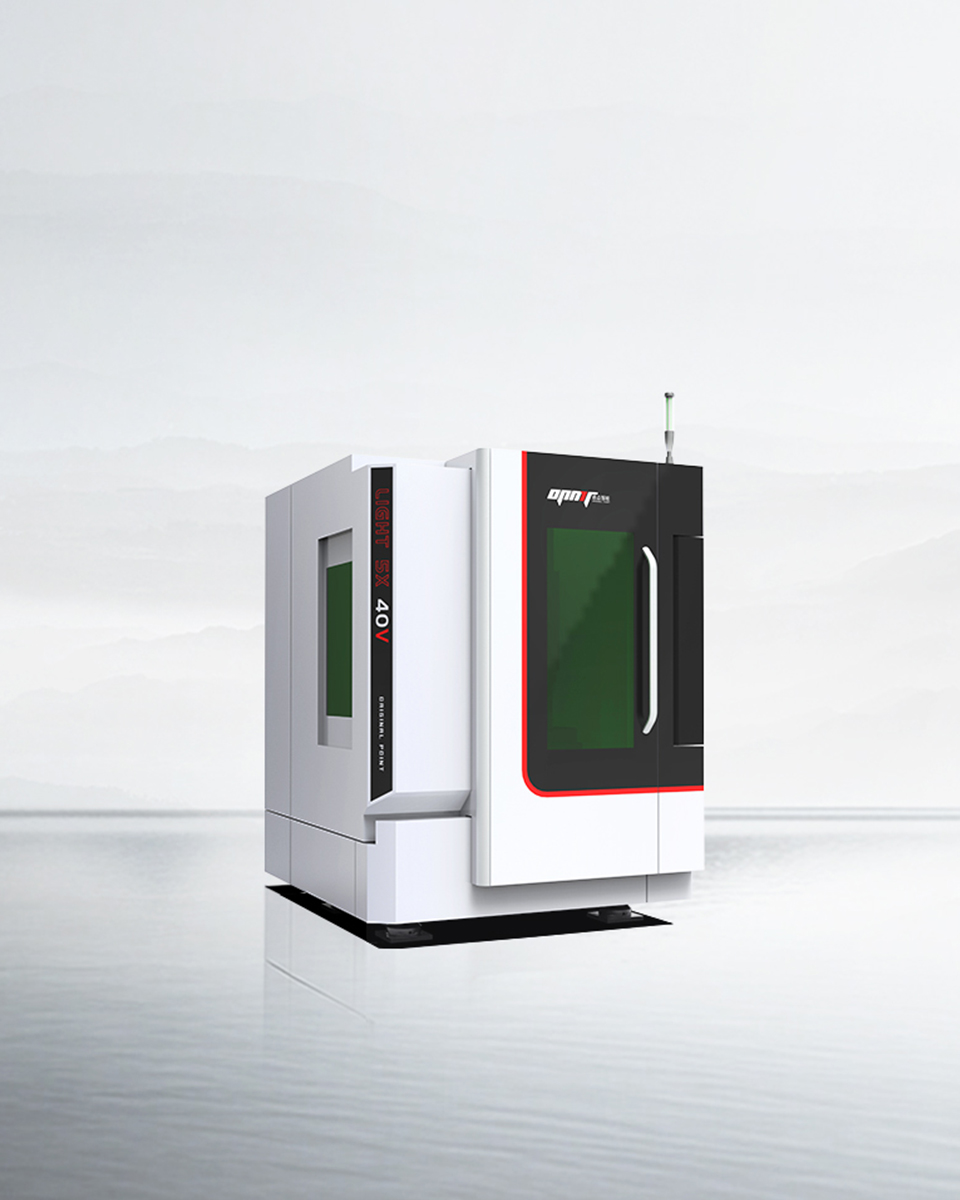
Light 5X 40V Technical Specifications:
- Positioning Accuracy: ±0.005mm for precision applications
- Repeatability: ±0.003mm ensuring consistent quality
- Laser Power: 100W suitable for both PA12 and PP processing
- Processing Speed: Up to 20 m/min depending on material and thickness
Light 5X 60V Enhanced Capabilities:
- Workbench Load Capacity: 300kg for larger components
- Tool Weight Capacity: Up to 25kg for complex tooling
- Processing Range: 600mm travel for larger workpieces
Surface Modification and Texturing
Laser texturing and surface modification technologies demonstrate particular advantages with both PA12 and PP materials. OPMT’s Micro3D L570V system enables complex surface patterns and microstructures that enhance functionality while maintaining processing efficiency.
L570V Texturing Capabilities:
- Processing Accuracy: 0.01mm precision for fine texture details
- 3D Modeling Integration: Direct processing from 3D model files
- Multi-Axis Processing: Five-axis capability for complex curved surfaces
- Environmental Benefits: No chemical pollution compared to traditional texturing
Material Selection Guidelines
Decision Framework
Based on OPMT’s engineering team evaluation criteria, material selection involves three critical factors: environmental conditions, mechanical demands, and budget constraints.
Choose PA12 when:
- High impact strength and mechanical performance are required
- Processing applications demand dimensional stability
- Chemical resistance to oils and solvents is necessary
- Additive manufacturing compatibility is important
Choose PP when:
- Moisture resistance is critical for application environment
- Cost optimization is the primary selection criterion
- Chemical stability in harsh environments is required
- Large-scale production economics favor lower material costs
Processing Optimization Strategies
Successful implementation requires careful consideration of processing parameters specific to each material. OPMT’s experience demonstrates that material-specific optimization delivers superior results compared to generic processing approaches.
PA12 Optimization Approach:
- Parameter development based on thermal stability characteristics
- Processing speed optimization for mechanical property retention
- Quality control focused on dimensional accuracy maintenance
PP Optimization Approach:
- Thermal management to prevent material distortion
- Power density control for consistent edge quality
- Parameter adjustment for thickness variation accommodation
Quality Standards and Compliance
Industry Standards Adherence
Both materials can achieve compliance with relevant industry standards when processed with appropriate parameters. OPMT’s laser processing systems maintain comprehensive certification compliance including CE marking, ISO 14001 environmental standards, and RoHS compliance for electronic applications.
Certification Requirements
OPMT’s manufacturing processes and equipment meet stringent quality standards:
- ISO 14001: Environmental management system certification
- ISO 45001: Occupational health and safety management
- RoHS Certification: Compliance for electronic component applications
Implementation Best Practices
Process Development Methodology
Phase 1: Material Assessment
- Thermal property evaluation for processing parameters
- Moisture content verification and control protocols
- Chemical compatibility assessment for processing environment
Phase 2: Parameter Optimization
- Initial processing trials with standard parameters
- Material-specific optimization based on quality requirements
- Process window definition for production consistency
Phase 3: Production Implementation
- Extended validation runs with production volumes
- Quality control system integration
- Operator training and procedure documentation
Technology Integration and Future Developments
Advanced Processing Capabilities
OPMT’s commitment to technological advancement continues to enhance processing capabilities for both PA12 and PP materials. The integration of advanced monitoring systems and adaptive control technologies enables real-time optimization for consistent quality outcomes.
Innovation Focus Areas:
- Automated parameter adjustment based on material response
- Real-time quality monitoring and feedback systems
- Process optimization through machine learning integration
- Enhanced surface modification capabilities
Conclusion and Recommendations
The selection between PA12 and PP for laser processing applications depends on specific requirements including mechanical properties, environmental conditions, and economic considerations. PA12 offers superior mechanical performance and chemical resistance, making it ideal for demanding applications in automotive and aerospace sectors. PP provides excellent moisture resistance and cost effectiveness, suitable for applications where these characteristics are prioritized.
OPMT’s advanced laser processing systems deliver optimized results for both materials through precise parameter control and comprehensive process monitoring. The combination of technical expertise, advanced equipment, and comprehensive support ensures successful implementation regardless of material selection.
Recommended OPMT Laser Solutions
For optimal PA12 and PP laser processing capabilities, OPMT offers comprehensive solutions:
- Light 5X 40V Vertical 5-Axis Laser Machining Center: Precision processing for 3C electronics and medical device applications with micron-level accuracy requirements
- Light 5X 60V Vertical 5-Axis Laser Machining Center: Enhanced capacity for automotive and industrial applications requiring maximum workpiece flexibility
- Micro3D L570V Mold Texturing System: Specialized surface texturing and microstructure processing for enhanced functionality and aesthetic appeal
Contact OPMT Laser’s technical specialists to explore how advanced laser processing technology can optimize your manufacturing operations with the most suitable material selection for your specific application requirements.
Disclaimer
This content is compiled by OPMT Laser based on publicly available information for reference only; mentions of third-party brands and products are for objective comparison and do not imply any commercial association or endorsement.