Five-axis laser manufacturing systems unite ultrafast photonics with precision motion engineering, enabling manufacturers to create features that conventional machining cannot approach. By synchronizing three linear axes with two rotary axes, these platforms position the laser focus within ±0.005 mm and maintain beam-quality factors (M²) below 1.3 across the full work envelope. Field data from OPMT’s 30,000 m² smart factory shows throughput gains exceeding 200% versus electrical-discharge machining while trimming per-unit costs by half. The following enterprise-level review explains how these results are achieved, which technical standards govern system design, and where the technology delivers measurable business value.
System Architecture and Kinematic Control
Optical–Mechanical Integration
Unlike fixed-beam stations, a five-axis architecture combines galvanometer scanners for micro-scale beam steering with servo-driven linear and rotary stages for macro positioning. Continuous feedback from linear encoders (resolution 0.0001 mm) and absolute rotary scales (resolution 0.36 arc-sec) feeds the real-time kernel, which solves inverse kinematics every 0.4 ms to keep the rotating tool center point (RTCP) locked on the programmed path. Adaptive optics compensate for thermal lensing so that focal spot dimensions remain constant, even under 24-hour duty cycles in ±1 °C controlled environments.
Motion Kernel and Interpolation
OPMT’s motion kernel executes jerk-limited, look-ahead interpolation that smooths axis reversals and virtually eliminates corner burrs. During a 13-axis simultaneous demonstration—XYZ, ABC, dual linear lasers, and ancillary handling axes—the controller maintained sub-nanometer path accuracy over 120,000 contour points. Independent verification with a laser interferometer confirmed cumulative path error below 3 µm on a 150 mm Inconel test spiral.
Laser Source Engineering
Ultrafast Pulse Dynamics
Material–light interaction shifts dramatically as pulse width changes. Femtosecond bursts (10⁻¹⁵ s) vaporize matter before heat diffuses, producing heat-affected zones (HAZ) under 50 µm—ideal for cardiovascular stents and microfluidics. Picosecond regimes (10⁻¹² s) balance edge quality with higher ablation rates, favored in SiC wafer dicing. Nanosecond sources (10⁻⁹ s) maximize removal volume for industrial marking and thick-section cutting. OPMT’s Light 5X platform allows hot-swapping of seed modules, giving engineers pulse-width agility without realigning the beam path.
Beam Quality and Power Stability
Across common medical-grade stainless steels, the Licht 5X 40V maintains an M² of 1.25 up to 300 W average power, verified using ISO 11146 methodology. Active power regulation holds output within ±2%, a prerequisite for FDA 21 CFR 1040 compliance when producing implantable devices. An integrated power meter triggers alarm states once drift exceeds 3%, protecting part quality and reducing scrap.
Precision and Performance Metrics
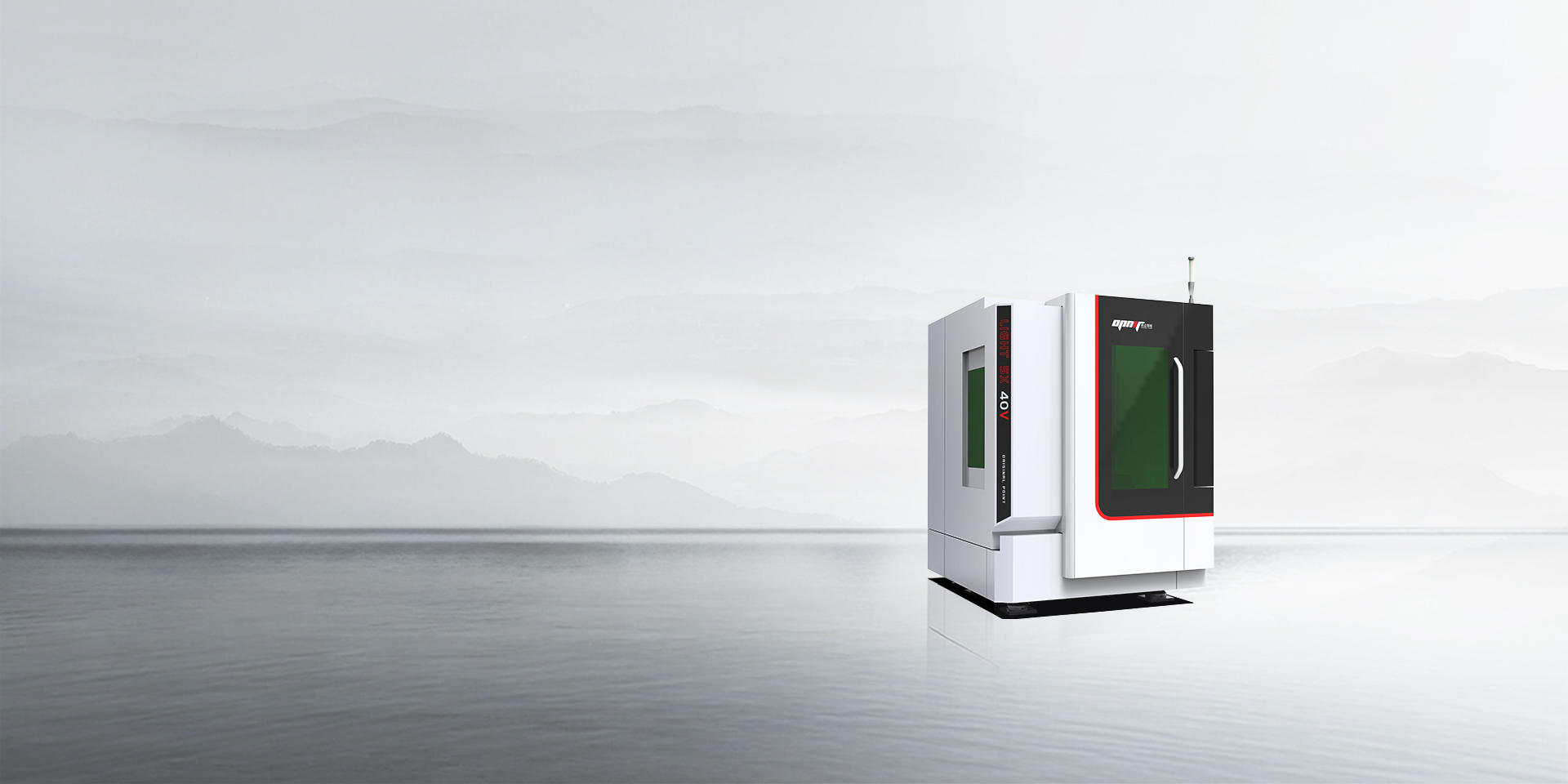
Leistungsmetrik | Licht 5X 40V | Licht 5X 60V | Measurement Method |
---|---|---|---|
Lineare Positioniergenauigkeit | ±0,005 mm | ±0,005 mm | ISO 230-2 laser interferometry |
Linear repeatability | ±0,003 mm | ±0,003 mm | Bidirectional cycles |
Rotary repeatability | ±5 arc-sec | ±5 arc-sec | Dual-ballbar test |
Maximum XYZ feed | 30 m min⁻¹ | 30 m min⁻¹ | Encoder trace |
Maximum C-axis speed | 300 rpm | 300 rpm | Encoder trace |
Beam quality (M²) | < 1.3 | < 1.3 | ISO 11146 profiling |
Thermal drift | < 0.0005 mm °C⁻¹ | < 0.0005 mm °C⁻¹ | Continuous probe |
These figures are audited quarterly as part of OPMT’s ISO 9001:2015 quality system, ensuring traceability for regulated sectors.
Application Case Studies
Cardiovascular Stent Production
At a tier-one medical OEM, a Light 5X 40V equipped with a 400-fs laser cut 316L nitinol tubing into 1.2 mm-diameter stents at 50 µm web thickness. The cycle time fell from 36 s (picosecond legacy line) to 18 s while eliminating chemical post-polish. Dimensional Cpk values exceeded 2.0 across 30,000 parts. Regulatory submission leveraged the machine’s built-in lot-level power and position logs, satisfying FDA design-history-file (DHF) requirements without additional instrumentation.
PCD Cutting Tool Manufacture
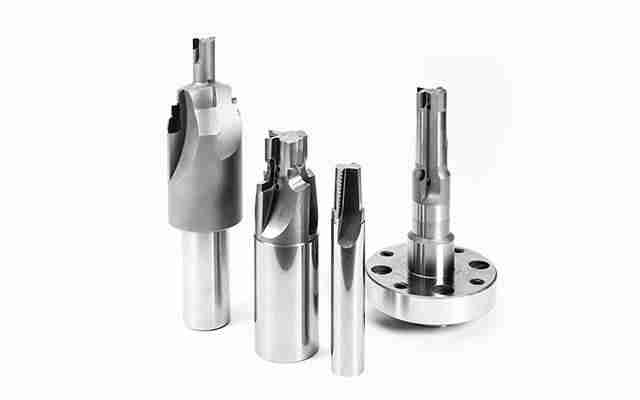
For a passenger-vehicle transmission program, an automotive supplier replaced EDM with a Light 5X 60V femtosecond system. Laser-fabricated chipbreakers held 0.003 mm profile tolerance and Ra 0.08 µm edge roughness. Tool life extended 2.4× in aluminum alloy milling, cutting annual insert spend by 39%.
SiC Power Wafer Dicing
A semiconductor foundry integrated two Light 5X 40V lines for 150 mm SiC wafers. Adaptive burst mode (17 × 20 ps) improved kerf edge chipping below 2 µm, meeting automotive AEC-Q101 reliability. Throughput reached 38 wafers h⁻¹, up from 22 wafers h⁻¹ on a single-axis UV laser saw, while energy per wafer dropped 28%.
Process Control and Quality Assurance
Echtzeitüberwachung
Coaxial vision captures melt-pool luminosity at 20 kHz, and a convolutional neural network flags anomalies—dross beads, plasma fluctuations, or focus shift—within 5 ms. The controller then modulates pulse energy or triggers a feed hold, preventing cumulative defects. Historical analysis shows 95% of previously scrap-bound parts are rescued by this closed-loop correction.
Dynamic Error Compensation
Temperature sensors on ball screws, drive motors, and granite bases feed a finite-element model that predicts growth vectors. Compensation values stream to the axis drives, countering drift to within 0.3 µm over eight-hour shifts. Ballbar plots taken every 500 hours confirm circularity remains inside ±3 µm, avoiding the quarterly mechanical tweaking once routine in conventional CNC shops.
Implementation Roadmap
Implementation follows a structured five-step methodology:
- Site Readiness Audit
Power stability must hold ±1% and floor vibration remain below 0.001 g RMS. Clean-room integration for Class 1000 airflow is recommended for medical and semiconductor programs. - Mechanical Installation and Calibration
Machines are anchored on 600 mm reinforced pads, leveled to 0.02 mm m⁻¹. Factory calibration uses interferometer mapping; user acceptance re-checks the same grid to prove identical performance. - Process Development
Application engineers tune pulse parameters, gas shielding, and path strategies. This phase typically runs three to four weeks for a new material family. - Validation and Documentation
Gauge R&R and process capability studies produce the statistical evidence required by ISO 13485 or AS9100 auditors. - Kontinuierliche Verbesserung
AI algorithms learn from production logs, recommending parameter tweaks that are verified in an offline sandbox before deployment.
A full greenfield installation reaches steady-state output in 8–10 weeks, although brownfield retrofits average six weeks by reusing HVAC and utilities.
Economic Analysis
A Light 5X 40V package—including femtosecond source, automated pallet changer, and vision QC—lists at USD 980 k. Annual ownership cost (service, optics, gas, depreciation) averages USD 142 k based on 4,400 runtime hours. In the PCD tool case, cash flow turned positive after 14 months; in stent manufacturing, the break-even point arrived in 19 months owing to lower production volume but higher part value. These projections exclude soft benefits such as reduced floor space and sustainability credits from chemical-free processing.
Compliance and Safety
All Light 5X platforms ship as Class 1 enclosed systems per IEC 60825-1, with redundant interlocks and door-status logic. Safety-related control functions conform to PL e / SIL 3. For US medical producers, embedded laser logs simplify 21 CFR 820 and 11 compliance during quality system inspections.
Future-Ready Features
OPMT’s latest firmware exposes OPC UA nodes for integration with MES and digital-twin applications. Edge computing modules preprocess sensor data, minimizing cloud latency for AI feedback loops. Upcoming releases will introduce blockchain certificate stamping, ensuring tamper-proof provenance for defense and implantable products.
Abschluss
Five-axis laser manufacturing systems transform complex geometry fabrication into a deterministic, lights-out process. By combining ultrafast photonics, high-fidelity kinematics, and real-time AI control, they deliver micron-level precision at industrial throughput, meeting the stringent demands of medical, aerospace, automotive, and semiconductor sectors. Organizations that deploy these platforms not only accelerate product launch cycles but also fortify quality assurance frameworks, positioning themselves at the forefront of smart, sustainable manufacturing.
Haftungsausschluss
Dieser Inhalt wurde von OPMT Laser auf Grundlage öffentlich verfügbarer Informationen zusammengestellt und dient ausschließlich zu Referenzzwecken. Die Erwähnung von Marken und Produkten Dritter dient dem objektiven Vergleich und stellt keine kommerzielle Verbindung oder Billigung dar.