Chemische Gasphasenabscheidung (CVD) hat die Diamantenherstellung revolutioniert und ermöglicht die Produktion hochwertiger synthetischer Diamanten mit präzise kontrollierten Eigenschaften für industrielle Anwendungen. Im Gegensatz zu natürlichen Diamanten, die über Millionen von Jahren unter extremen geologischen Bedingungen entstehen, werden CVD-Diamanten in kontrollierten Laborumgebungen mithilfe hochentwickelter Reaktorsysteme hergestellt. Diese synthetischen Diamanten weisen außergewöhnliche mechanische, thermische und optische Eigenschaften auf, die sie für zahlreiche Hightech-Branchen wertvoll machen.
OPMT Laser hat sich als führender Anbieter fortschrittlicher Laserbearbeitungslösungen für im Labor gezüchtete Diamanten etabliert und bietet Spezialgeräte für die besonderen Herausforderungen bei der Bearbeitung dieser superharten Materialien. Mit ISO 9001:2015-Zertifizierung und mehreren Innovationspreisen im Bereich Lasertechnologie liefert OPMT Präzisionsbearbeitungssysteme, die Roh-CVD-Diamanten in Komponenten mit außergewöhnlicher Maßgenauigkeit und Oberflächenqualität verwandeln.
Herausforderungen bei der CVD-Diamantproduktion und -verarbeitung
Produktionstechnologie Übersicht
Bei der CVD-Diamantsynthese werden Kohlenstoffatome unter spezifischen Temperatur-, Druck- und Gaszusammensetzungsbedingungen sorgfältig kontrolliert auf einem Substrat abgeschieden. Dabei entstehen Diamantmaterialien mit unterschiedlichen Kristallstrukturen:
- Einkristalliner CVD-Diamant: Höchste Qualität mit gleichmäßiger Kristallstruktur
- Polykristalliner CVD-Diamant: Enthält mehrere Kristalldomänen mit definierten Grenzen
- Nanokristalliner Diamant: Sehr kleine Kristallkörner (<100 nm) mit speziellen Eigenschaften
Nach der Herstellung dieser Materialien sind anspruchsvolle Verarbeitungstechniken erforderlich, um sie in nutzbare Komponenten mit präzisen Geometrien und Oberflächeneigenschaften umzuwandeln, die für industrielle Anwendungen erforderlich sind.
Einschränkungen der traditionellen Verarbeitung
Herkömmliche Methoden der Diamantverarbeitung stehen vor erheblichen Herausforderungen:
Verarbeitungsmethode | Einschränkungen bei CVD-Diamanten |
---|---|
EDM (Elektroerosion) | – Absplitterungen und Risse an Schnittkanten – Nichtleitende Materialien können nicht verarbeitet werden – Langsame Verarbeitungsgeschwindigkeit (1 mm/min) |
Mechanisches Schleifen | – Schneller Werkzeugverschleiß – Eingeschränkte Präzision – Schwierigkeiten mit komplexen Geometrien |
Chemisches Ätzen | – Schlechte Maßkontrolle – Umweltbedenken – Begrenzte Materialabtragsrate |
Wie im technischen Vergleich von OPMT angemerkt wird: „Bei der Verarbeitung großer Partikel oder polykristalliner Diamanten mit geringer Leitfähigkeit kommt es zu Drahtsprüngen und die Bearbeitung kann mit herkömmlichen EDM-Methoden nicht fortgesetzt werden“, was den Bedarf an fortschrittlichen Laserverarbeitungslösungen unterstreicht.
Diamantverarbeitungslösungen von OPMT Laser
DiaCUT L315V: Spezialisierte CVD-Diamantoberflächenbearbeitung
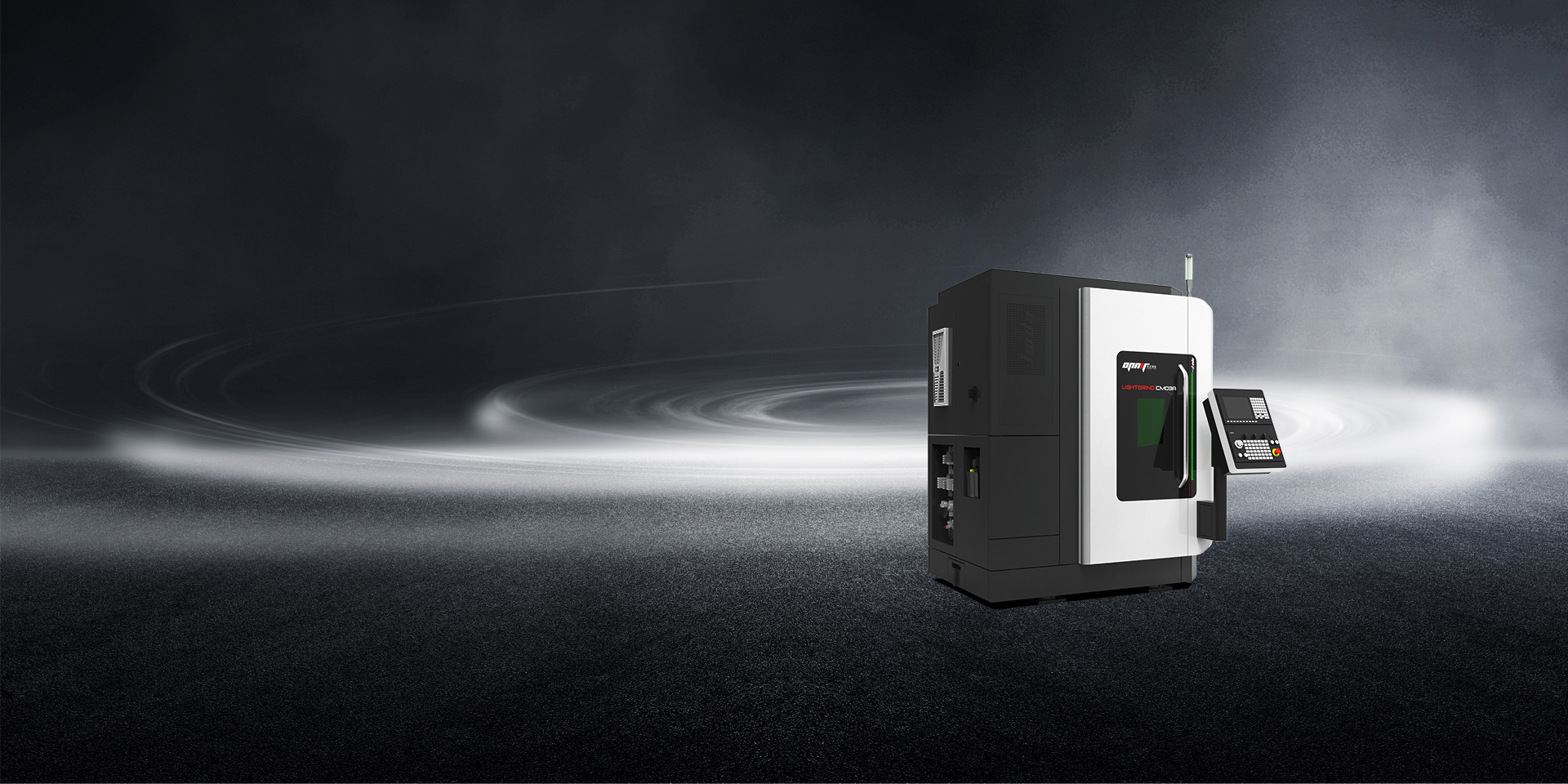
Der DiaCUT L315V CVD-Laser-Diamant-Oberflächenschleifmaschine stellt die spezielle Lösung von OPMT für die hochpräzise Diamantoberflächenbearbeitung dar. Dieses System bietet:
Technische Spezifikationen:
- X-Achsen-Verfahrweg: 300 mm
- Y-Achsen-Verfahrweg: 100 mm
- Z-Achsen-Verfahrweg: 100 mm
- Wellenlänge: 532 nm (grüner Laser)
- Positioniergenauigkeit: 0,01 mm
- Wiederholgenauigkeit: 0,002 mm
- Strombedarf: 20 A (AC220 V ± 101 TP3T)
Diese Spezialmaschine wurde speziell für Diamantanwendungen entwickelt und verfügt über eine präzise Linienparallelitätserkennung und Laserinterferometer-Kalibrierungsfunktionen, die für die Produktion hochwertiger Diamantkomponenten unerlässlich sind.
Light 5X-Serie: Mehrachsige Bearbeitung komplexer Diamantkomponenten
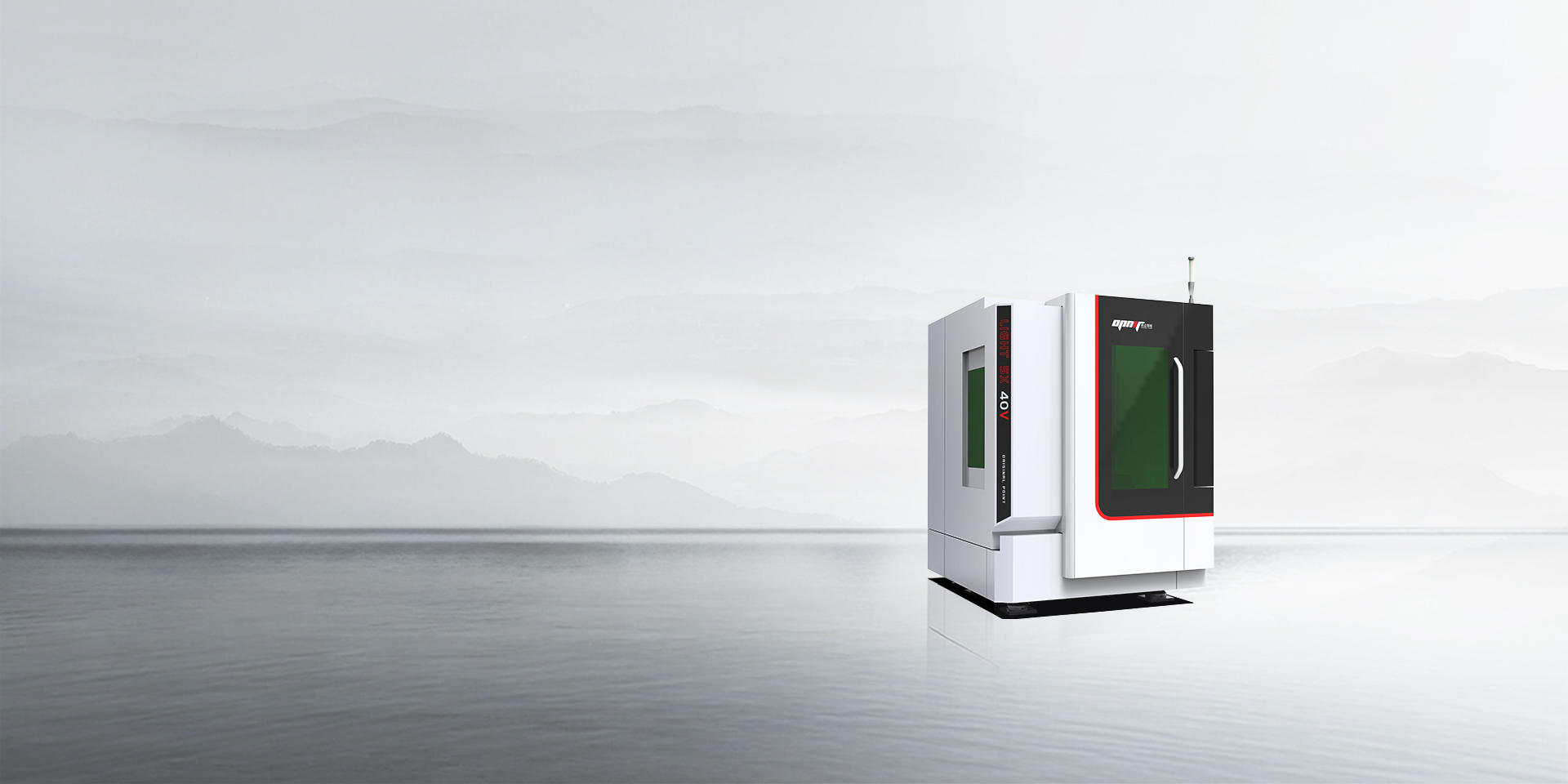
Für komplexere Diamantverarbeitungsanwendungen bietet OPMT die Licht 5X 40V Und Licht 5X 60V vertikale 5-Achsen-Laserbearbeitungszentren, die sich durch die Bearbeitung von Diamantmaterialien wie PCD, CBN und CVD-Diamant mit beispielloser Präzision auszeichnen.
Wichtige Spezifikationen:
- Positioniergenauigkeit: 0,005 mm (5 Mikrometer)
- Wiederholgenauigkeit der Positionierung: 0,003 mm
- Fortschrittliche Linearmotor-Antriebssysteme
- B/C-Achsen-Positionierung: 10″/5″
- Laserpulsbreite: 1–100 ns
- RTCP (Rotational Tool Center Point) 5-Achsen-Verbindungsfähigkeit
In der technischen Dokumentation von OPMT heißt es: „Diese Maschine wird häufig zur Bearbeitung von PCD, CBN, Hartlegierungen, Keramik, Metall und anderen Materialien verwendet und kann komplexe Konturen und Profile von Fräsern mit geschweißter Kante, Mikrokantenwerkzeugen und dünnwandigen Metallteilen bearbeiten.“
Technische Vorteile der Laserbearbeitung von CVD-Diamant
Überlegene Verarbeitungsleistung
Die Laserbearbeitung bietet gegenüber herkömmlichen Verfahren zur CVD-Diamantbearbeitung erhebliche Vorteile:
Leistungsmetrik | Traditionelles EDM | OPMT Lasersysteme | Verbesserung |
---|---|---|---|
Verarbeitungsgeschwindigkeit | 1 mm/min | Bis zu 3,0 mm/min | 3× schneller |
Kantenqualität | Absplitterungen und Risse sind üblich | Kein Kantenabsplittern bei 200-facher Vergrößerung | Überragende Qualität |
Materialflexibilität | Nur leitfähige Materialien | Alle Diamantarten, einschließlich nichtleitender CVD | Erweiterte Funktionen |
Verarbeitungsgenauigkeit | ≥0,015 mm | ≤0,005 mm | 3× besser |
Wärmeeinflusszone | Bedeutsam | Minimal (<5μm mit Femtosekunden) | Überlegene Erhaltung der Materialeigenschaften |
Durch die berührungslose Art der Laserbearbeitung wird der Werkzeugverschleiß vermieden, während gleichzeitig eine gleichbleibende Qualität mit „Kantenpassivierungsmöglichkeiten von 0,004–0,005 mm“ und einer „Oberflächenrauheit von weniger als 0,1 μm“ für Diamantmaterialien gewährleistet wird.
Fortschrittliche Steuerungssysteme und Software
Die Diamantverarbeitungssysteme von OPMT verfügen über hochentwickelte Steuerungstechnologien:
- NUM CNC-Steuerungssystem sorgt für maximalen Bedienkomfort und Prozesssicherheit
- GTR-Schneidwerkzeugsoftware bietet einen einfachen Übergang von der Funkenerosion zur Laserbearbeitung durch:
- Branchenübliche Programmierlösungen ermöglichen den Import vorhandener EDM-Projekte
- Parametrisierte Software für rotierende und feste Werkzeuge
- Automatische 3D-Vermessung von Diamantoberflächen
- Automatische Programmgenerierung mit direkter Maschinensimulation
Die Integration von RTCP (Rotationaler Werkzeugmittelpunkt) Durch die 5-Achsen-Verbindungstechnologie können die Maschinen bei der Ausführung komplexer mehrachsiger Bewegungen eine präzise Werkzeugpositionierung relativ zu den Werkstücken beibehalten – eine wesentliche Voraussetzung für die Erstellung komplexer Merkmale in Diamantkomponenten.
Industrielle Anwendungen von verarbeitetem CVD-Diamant
Halbleiter und Elektronik
Aufgrund seiner außergewöhnlichen Wärmeleitfähigkeit eignet sich CVD-Diamant ideal für elektronische Anwendungen, bei denen das Wärmemanagement von entscheidender Bedeutung ist:
- Wärmeverteiler für elektronische Hochleistungsgeräte
- Kühlkörper für Halbleiterlaser und LEDs
- Substrate für GaN-Leistungsbauelemente
- Fenster für Hochleistungs-HF-Geräte
Der 3C Electronic Digitale Branchenlösungen Die von OPMT angebotenen Verfahren ermöglichen die präzise Verarbeitung von Diamantkomponenten für diese Anwendungen mit Maßtoleranzen von bis zu 0,003 mm.
Automobilanwendungen
Im Automobilsektor bieten verarbeitete Diamantkomponenten eine außergewöhnliche Verschleißfestigkeit und hervorragende Wärmemanagementfähigkeiten:
- Schneidwerkzeuge für die Bearbeitung von Automobilkomponenten
- Verschleißfeste Lager und Buchsen
- Wärmeverteiler für die Leistungselektronik in Elektrofahrzeugen
- Spezialkomponenten für Hochleistungsmotoren
OPMTs Lösungen für die Automobil- und Teileindustrie Gehen Sie mit speziellen Laserverarbeitungsfunktionen auf diese Anwendungen ein.
Präzisionswerkzeug- und Schneidanwendungen
Aufgrund seiner überragenden Härte ist Diamant das Material der Wahl für Schneid- und Bearbeitungsanwendungen:
- PKD-Schneidwerkzeuge (Polykristalliner Diamant)
- CVD-Diamantbeschichtete Bohrer und Schaftfräser
- Diamant-Abrichtwerkzeuge für Schleifscheiben
- Diamantziehsteine zum Drahtziehen
Die mit den Lasersystemen von OPMT erreichte Präzision ermöglicht „den Zahnabschnitt eines Bodenschneiders“ und andere spezielle Werkzeuganwendungen, die eine außergewöhnliche Kantenqualität und Maßgenauigkeit erfordern.
Optische und photonische Anwendungen
Die breite optische Transparenz von CVD-Diamanten macht ihn für spezielle optische Anwendungen wertvoll:
- Optische Infrarotfenster
- Hochleistungslaserfenster
- Optische Sensoren
- Quantenphotonische Geräte
Die Präzisionslaserverarbeitungsfähigkeiten von OPMT ermöglichen die Herstellung optischer Komponenten mit einer „Oberflächenrauheit von weniger als 0,1 μm“ und einer „Konturgenauigkeit von weniger als 10 μm“, was für optische Hochleistungsanwendungen unerlässlich ist.
Qualitätskontroll- und Verifizierungssysteme
OPMT implementiert umfassende Qualitätssicherungsprotokolle für die Diamantverarbeitung:
- Präzisionsprüfgeräte:
- Erkennung der Parallelitätsgenauigkeit der X-/Y-/Z-Achse
- B/C-Achsen-Parallelitätsgenauigkeitserkennung
- Präzise Erkennung der Linienparallelität
- Kreisformprüfung zur Bestimmung der Kreisgenauigkeit
- Validierung des Ausrichtungslasers
- Überprüfung des Drehachsenkalibrators
- Laserstrahlprofilanalyse
- Laserinterferometermessung
- Branchenzertifizierungen:
- ISO 9001:2015-Zertifizierung
- Umweltmanagementsystem ISO 14001
- ISO 45001 Arbeitsschutzmanagementsystem
- RoHS-Zertifizierung
Diese strengen Test- und Zertifizierungssysteme gewährleisten eine gleichbleibende Qualität bei der Verarbeitung von Diamantkomponenten über alle Produktionsläufe hinweg.
Zukünftige Entwicklungen in der Diamantverarbeitungstechnologie
OPMT verbessert seine Diamantverarbeitungskapazitäten durch verschiedene Innovationen kontinuierlich:
- Multi-Laser-Verbundbearbeitungstechnologie kombiniert Nanosekunden-, Pikosekunden- und Femtosekunden-Laserquellen für optimierten Materialabtrag und Oberflächenbearbeitung
- Wassergeführte Lasertechnologie unter Verwendung der WJC532V Wassergeführtes Laser-Fünf-Achsen-Bearbeitungszentrum für verbesserte Präzision und reduzierte thermische Effekte
- Femtosekundenlaser-Behandlung für die „Kaltverarbeitung“, die thermische Schäden an Diamantmaterialien minimiert und kritische Materialeigenschaften bewahrt
- KI-gesteuerte Parameteroptimierung unter Verwendung Die fortschrittlichen Softwarelösungen von OPMT die Verarbeitungsparameter basierend auf Materialeigenschaften und gewünschten Ergebnissen kontinuierlich zu verfeinern
Abschluss
Die CVD-Diamanttechnologie stellt einen revolutionären Fortschritt in der Materialwissenschaft dar und findet Anwendung in der Elektronik-, Automobil-, Werkzeug- und optischen Industrie. Die fortschrittlichen Diamantbearbeitungssysteme von OPMT Laser überwinden die Grenzen traditioneller Bearbeitungsmethoden und bieten beispiellose Präzision, Effizienz und Qualität selbst für anspruchsvollste Diamantkomponentenanwendungen.
Zu den wichtigsten technischen Vorteilen gehören:
- Höchste Präzision: Erreichen einer Positioniergenauigkeit von 0,005 mm und einer Wiederholgenauigkeit von 0,003 mm, wodurch komplexe Geometrien möglich werden, die mit herkömmlichen Methoden nicht möglich sind
- Prozesseffizienz: Bis zu 3-mal schnellere Verarbeitungsgeschwindigkeiten als bei herkömmlichen EDM-Methoden, gleichzeitiger Wegfall von Verbrauchsmaterialien und Reduzierung der Umweltbelastung
- Materialvielfalt: Fähigkeit zur Verarbeitung aller Arten von CVD-Diamanten, einschließlich nichtleitender Sorten, die mit herkömmlichem EDM nicht bearbeitet werden können
- Verbesserte Kantenqualität: Perfekte Schneidkanten ohne Absplitterungen oder Risse, selbst bei 200-facher Vergrößerung, entscheidend für Hochleistungs-Werkzeuganwendungen
- Reduzierte Betriebskosten: Bis zu 53% niedrigere monatliche Betriebskosten im Vergleich zu herkömmlichen Methoden
Da synthetischer Diamant in den Hochtechnologiebranchen immer mehr an Bedeutung gewinnt, ermöglichen die spezialisierten Diamantverarbeitungssysteme von OPMT Laser den Herstellern, die außergewöhnlichen Eigenschaften dieses bemerkenswerten Materials voll auszunutzen und gleichzeitig die Präzision und Qualität zu erreichen, die für die anspruchsvollsten Anwendungen erforderlich ist.
Haftungsausschluss
Dieser Inhalt wurde von OPMT Laser auf Grundlage öffentlich verfügbarer Informationen zusammengestellt und dient ausschließlich zu Referenzzwecken. Die Erwähnung von Marken und Produkten Dritter dient dem objektiven Vergleich und stellt keine kommerzielle Verbindung oder Billigung dar.