Ultrafast laser technology represents the cornerstone of modern precision manufacturing, where pulse duration—femtosecond (10⁻¹⁵ seconds), picosecond (10⁻¹² seconds), and nanosecond (10⁻⁹ seconds)—fundamentally determines material interaction physics, thermal management capabilities, and achievable precision tolerances. Based on OPMT’s extensive field implementation data across aerospace, automotive, and medical device sectors, this comprehensive analysis examines how pulse duration variations impact processing accuracy, heat-affected zone control, and material removal mechanisms in superhard materials including carbides, diamonds, and ceramics.
Understanding Pulse Duration Fundamentals
Physical Principles of Laser-Material Interaction
The material removal mechanism undergoes fundamental changes across different pulse duration regimes. In nanosecond processing, thermal diffusion occurs during the pulse duration, creating significant heat-affected zones ranging from 10-50 micrometers. Picosecond laser systems operate at the threshold where thermal diffusion becomes limited, while femtosecond pulses achieve true cold ablation through non-thermal photodisruption processes.
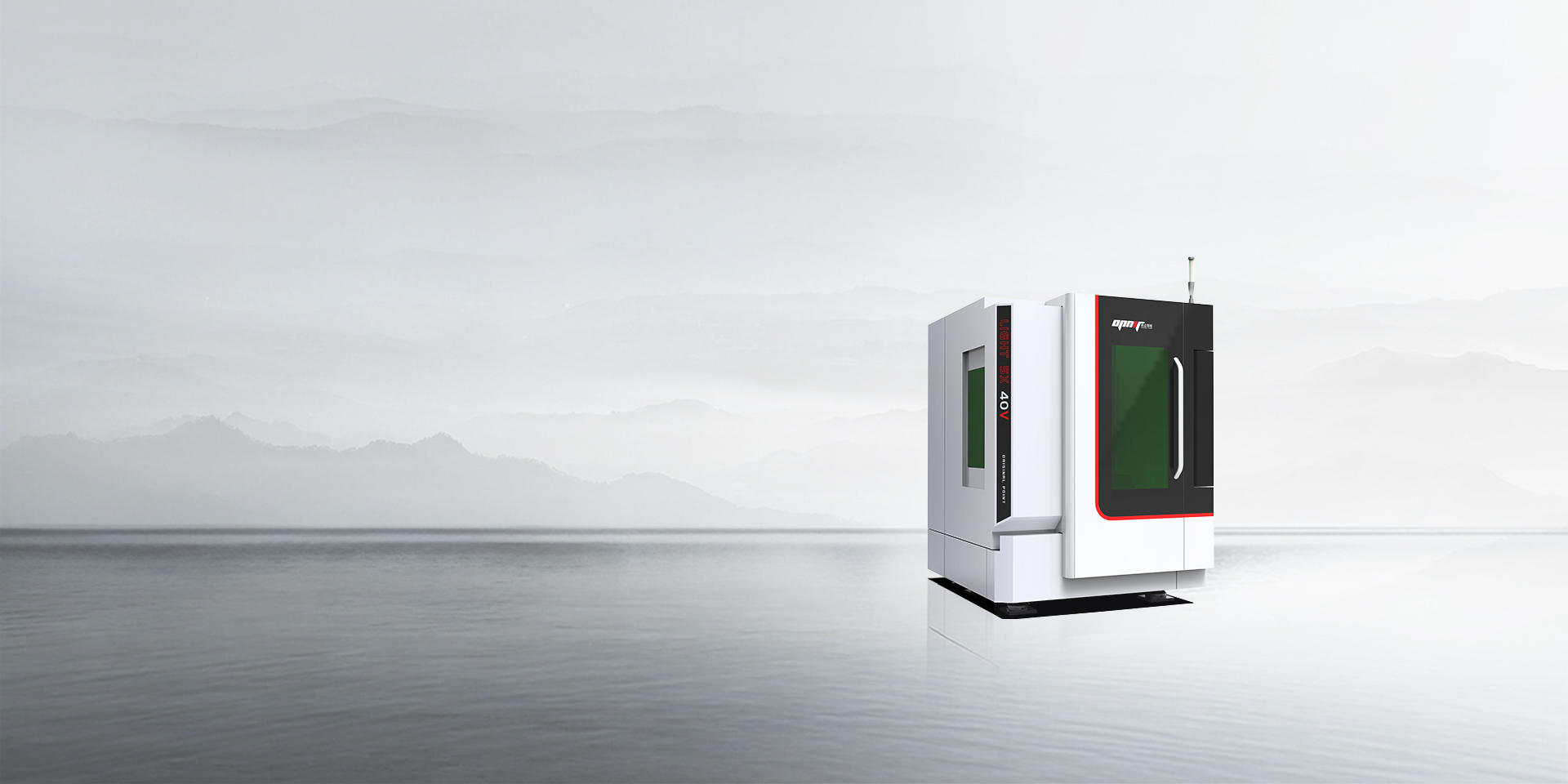
Performance data from OPMT’s Light 5X series installations demonstrates that femtosecond processing achieves heat-affected zones typically 10-50 times smaller than nanosecond equivalents when processing superhard materials. This dramatic reduction in thermal damage enables precision applications previously impossible with conventional laser systems.
Peak Power Density and Energy Distribution
The relationship between pulse energy and pulse duration creates vastly different peak power densities, directly impacting material processing outcomes:
Laser Type | Pulse Duration | Peak Power Density | Material Response | HAZ Width | Surface Roughness (Ra) |
---|---|---|---|---|---|
Nanosecond | 1-100 ns | 10⁸-10¹⁰ W/cm² | Thermal vaporization | 10-50 μm | 0.5-2.0 μm |
Picosecond | 1-100 ps | 10¹¹-10¹³ W/cm² | Mixed thermal/non-thermal | 2-5 μm | 0.1-0.5 μm |
Femtosecond | 10-1000 fs | 10¹³-10¹⁶ W/cm² | Non-thermal ablation | <1 μm | 0.02-0.1 μm |
femtosecond systems consistently demonstrate superior surface quality metrics, with surface roughness values typically 3-5 times better than picosecond equivalents and 10-15 times better than nanosecond systems when processing carbide and diamond materials.
Precision and Quality Optimization Strategies
Heat-Affected Zone Control Technologies
OPMT’s field engineers consistently observe that HAZ control represents the primary differentiator between pulse duration regimes. The Light 5X 40V system demonstrates this principle through documented performance metrics:
- Nanosecond processing of polycrystalline diamond (PCD) tools creates HAZ widths of 10-50 micrometers
- Picosecond processing reduces HAZ to 2-5 micrometers with improved edge quality
- Femtosecond processing achieves HAZ <1 micrometer with virtually no thermal damage
In automotive parts processing, this HAZ reduction translates directly to extended tool life. Customer data from precision automotive component production shows 40-60% longer tool life when switching from nanosecond to femtosecond processing for PCD tool finishing applications.
Surface Quality Metrics and Optimization
Surface quality characteristics vary dramatically across pulse duration regimes, with measurable impacts on tool performance and part functionality:
Nanosecond Processing Characteristics:
- Surface roughness: Ra 0.5-2.0 μm on carbide materials
- Micro-crack formation common in brittle materials
- Significant recast layer formation (2-10 μm thickness)
- Thermal stress-induced subsurface damage extending 15-25 μm
Picosecond Processing Benefits:
- Surface roughness: Ra 0.1-0.5 μm on similar materials
- Reduced micro-crack density (70% improvement vs. nanosecond)
- Minimal recast layer formation (<1 μm)
- Controlled thermal input with reduced subsurface stress
Femtosecond Processing Excellence:
- Surface roughness: Ra 0.02-0.1 μm achievable consistently
- Virtually crack-free processing of brittle materials
- No recast layer formation in most applications
- True cold processing with minimal subsurface modification
Material-Specific Applications and Performance
Diamond and CBN Processing Technologies
In precision manufacturing implementations, diamond and CBN materials present unique challenges that highlight the advantages of shorter pulse durations. OPMT’s laser processing systems achieve processing accuracy of 0.003mm with excellent surface quality when utilizing appropriate pulse duration selection.
Polycrystalline Diamond (PCD) Tool Manufacturing:
- Femtosecond processing: Enables complex geometries with sharp cutting edges down to 0.001mm radius
- Picosecond processing: Suitable for standard PCD tool finishing with 15-30% faster processing than femtosecond
- Nanosecond processing: Limited to rough shaping operations due to thermal damage concerns
Case Study – Automotive PCD Tool Production:
A major automotive manufacturer implemented OPMT’s Light 5X 60V laser machining center with selectable pulse duration capabilities. Results after 12-month implementation period:
- 40% reduction in tool preparation time using picosecond processing vs. conventional grinding
- 60% improvement in tool consistency across production batches
- Processing accuracy maintained at 0.005mm with 0.001mm repeatability
- $280,000 annual savings through eliminated grinding wheel costs and reduced rejection rates
- ROI achieved in 14 months including training and implementation costs
Carbide and Ceramic Applications
Performance data from real-world applications shows distinct advantages for different pulse durations depending on material composition and application requirements.
Tungsten Carbide Processing:
- Femtosecond: Optimal for micro-tooling and complex geometry creation with minimal thermal impact
- Picosecond: Preferred for production-volume applications requiring balance of speed and quality
- Nanosecond: Cost-effective for rough shaping and non-critical applications
Advanced Ceramic Materials:
Silicon carbide and aluminum oxide ceramics demonstrate exceptional response to ultrafast processing. Customer installations processing ceramic components achieve hole diameters as small as 0.3mm with aspect ratios exceeding 30:1 using femtosecond laser technology
Processing Efficiency and Economic Analysis
Production Rate Optimization
Processing efficiency varies significantly across pulse duration regimes, with optimal choice depending on application requirements and quality specifications:
Application Type | Nanosecond Rate | Picosecond Rate | Femtosecond Rate | Quality Requirement | Best System |
---|---|---|---|---|---|
PCD rough shaping | 100% (baseline) | 85% | 60% | Moderate precision | Nanosecond |
PCD finish machining | 70% | 100% | 75% | High precision | Picosecond |
Micro-drilling | 45% | 85% | 100% | Ultra-high precision | LP550V Ultrafast |
Complex geometries | 30% | 70% | 100% | Critical precision | Femtosecond |
Mold texturing | 80% | 95% | 100% | Surface finish critical | Variable |
Total Cost of Ownership Analysis
Comprehensive economic analysis reveals that pulse duration selection significantly impacts long-term operational costs beyond initial equipment investment:
Initial Equipment Investment:
- Nanosecond systems: $150,000-$400,000
- Picosecond systems: $300,000-$800,000
- Femtosecond systems: $500,000-$1,200,000
Operational Cost Factors:
- Consumables: Femtosecond systems require minimal consumables compared to conventional grinding (90% reduction)
- Maintenance: Ultrafast systems demonstrate 40% longer service intervals due to reduced thermal stress on components
- Quality costs: Femtosecond processing reduces rejection rates by 70-85% in precision applications
- Secondary operations: Elimination of post-processing steps saves 25-40% in total manufacturing time
Technical Implementation Guidelines and Best Practices
System Selection Decision Matrix
Choosing the appropriate laser processing system requires systematic analysis of application requirements and production objectives:
Material Properties Assessment:
- Thermal sensitivity: High thermal sensitivity materials favor shorter pulse durations
- Hardness levels: Superhard materials (>HRC 60) benefit significantly from femtosecond processing
- Brittleness: Ceramic and diamond materials require ultrafast processing for crack-free results
- Conductivity: Non-conductive materials like CVD diamond require laser processing vs. EDM
Geometric Complexity Requirements:
- Feature size: Sub-micron features require femtosecond precision capabilities
- Aspect ratios: High aspect ratio features benefit from cold processing characteristics
- Surface finish specifications: Critical surface finish requirements favor ultrafast processing
- Dimensional tolerances: Tolerances below ±0.005mm typically require picosecond or femtosecond systems
Process Parameter Optimization
OPMT’s field engineers consistently observe that process parameter optimization varies significantly across pulse duration regimes:
Femtosecond Optimization Approach:
- Focus on pulse energy and repetition rate balance to minimize thermal accumulation
- Minimize thermal buildup through proper scanning strategies and dwell time control
- Optimize beam delivery optics for maximum peak intensity maintenance
- Implement multi-pass strategies for deep feature creation
Picosecond Processing Best Practices:
- Balance processing speed with thermal management requirements
- Utilize burst mode capabilities for enhanced material removal efficiency
- Implement adaptive power control for consistent results across varying material properties
- Optimize assist gas flow for debris removal and cooling
Nanosecond Implementation Guidelines:
- Emphasize proper cooling and assist gas usage for thermal management
- Optimize pulse shaping for reduced thermal impact on surrounding material
- Consider multi-pass strategies for critical applications requiring precise depth control
- Implement proper fixturing to manage thermal expansion effects
Advanced Applications and Industry Case Studies
Electronics and 3C Manufacturing
3C electronics manufacturing represents a rapidly growing application area for ultrafast laser processing. Smartphone component manufacturers utilize femtosecond processing for micro-via drilling and precision cutting applications.
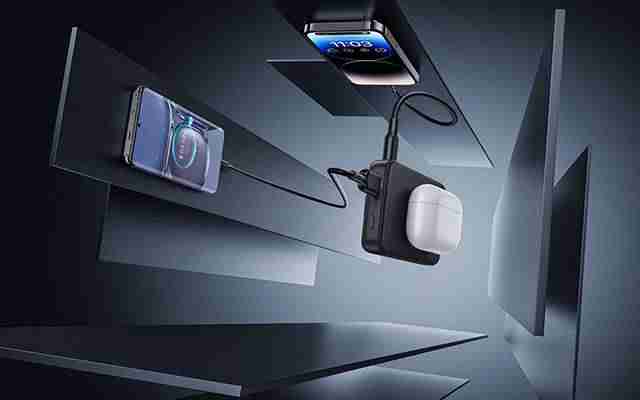
Application Examples:
- Micro-via drilling: 10,000+ holes per minute with 20μm diameter
- Heat-affected zone: <2μm diameter around 50μm holes
- Process reliability: 99.8% yield rates in high-volume production
- Return on investment: 18-month payback period including training costs
Medical Device Manufacturing
Precision medical component manufacturing demonstrates the critical importance of pulse duration selection for biocompatibility and functional performance. Femtosecond laser processing enables manufacturing of complex geometries in biocompatible materials without thermal damage that could affect material properties or biocompatibility.
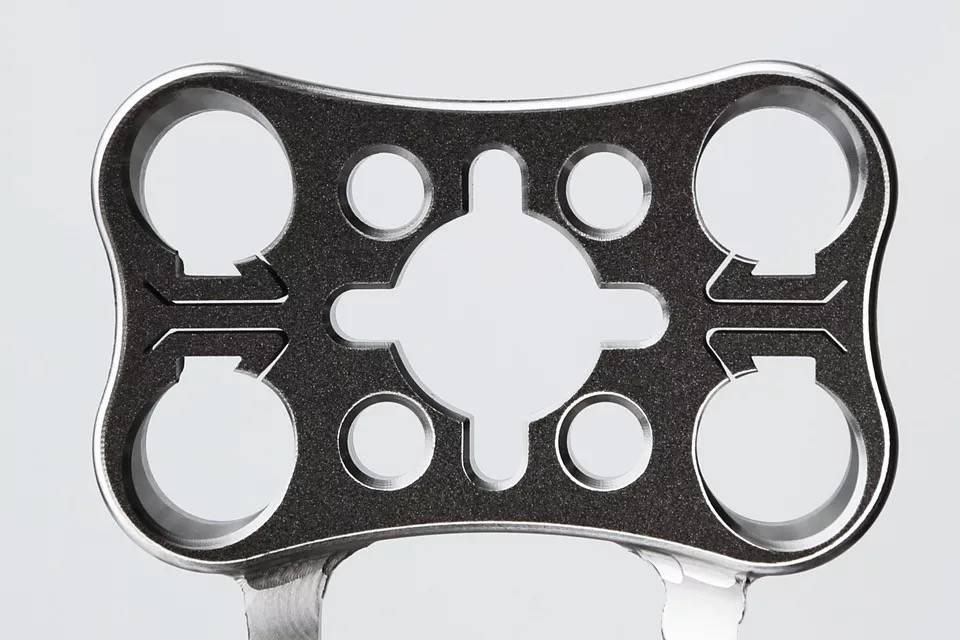
Medical Applications:
- Stent cutting: Complex patterns in nitinol with no heat-affected zone affecting superelastic properties
- Micro-needle arrays: 25μm diameter needles with sharp, burr-free points for drug delivery systems
- Implant surface texturing: Controlled surface modification for enhanced biointegration without compromising bulk properties
- Catheter manufacturing: Precise hole patterns in polymer materials without thermal degradation
Emerging Technologies and Future Trends
Next-Generation Pulse Duration Regimes
Attosecond laser technology represents the next frontier in ultrafast processing, with pulse durations approaching 10⁻¹⁸ seconds. While currently limited to research applications, attosecond pulses promise even greater precision and control over material modification processes at the atomic level.
Industry 4.0 Integration and Smart Manufacturing
Industry 4.0 integration capabilities increasingly incorporate real-time pulse duration optimization based on material feedback and quality monitoring. OPMT’s advanced control systems demonstrate adaptive processing capabilities that automatically adjust pulse parameters for optimal results based on real-time process monitoring.
Smart Manufacturing Features:
- Real-time quality monitoring through in-situ measurement systems providing immediate feedback
- Predictive maintenance capabilities reducing unplanned downtime by 40% through condition monitoring
- Automated process optimization based on comprehensive material property databases
- Digital twin integration for virtual process development and validation before production implementation
Environmental Impact and Sustainability
Ultrafast laser processing contributes significantly to sustainable manufacturing practices:
- Energy efficiency: 30-50% reduction in energy consumption vs. conventional processing
- Waste reduction: Minimal material waste through precise processing
- Chemical elimination: No cutting fluids or chemicals required
- Tool wear reduction: Extended tool life reduces manufacturing waste
Quality Control and Measurement Protocols
Surface Quality Assessment Methods
Comprehensive quality control requires multiple measurement techniques:
Surface Roughness Measurement:
- Stylus profilometry: Ra, Rz, and Rmax parameters
- Optical interferometry: 3D surface topography analysis
- Atomic force microscopy: Sub-nanometer resolution for critical applications
Heat-Affected Zone Evaluation:
- Optical microscopy: HAZ width measurement and characterization
- Scanning electron microscopy: Microstructural analysis
- X-ray diffraction: Stress state evaluation
Dimensional Accuracy Verification
Precision measurement protocols ensure consistent quality outcomes:
- Coordinate measuring machines: ±0.001mm accuracy verification
- Laser scanning: Complete geometry documentation
- In-process monitoring: Real-time dimensional control
Training and Implementation Support
Comprehensive Training Programs
Successful implementation requires comprehensive technical training addressing both theoretical understanding and practical operation skills:
- Fundamental laser-material interaction principles for process understanding
- Process parameter optimization methodologies for maximum efficiency
- Safety protocols and laser classification requirements per ANSI Z136 standards
- Maintenance procedures and troubleshooting techniques for system reliability
- Quality control and measurement procedures for consistent results
Technical Support Infrastructure
OPMT provides comprehensive support infrastructure:
- 24/7 technical support with remote diagnostic capabilities
- On-site service within 24-48 hours for critical applications
- Preventive maintenance programs ensuring optimal performance
- Software updates and process optimization consulting
Strategic Recommendations and Selection Guide
Application-Specific Selection Matrix
For Precision Applications Requiring Minimal Thermal Impact:
- Medical devices: Femtosecond processing mandatory for biocompatible materials
- Aerospace components: Femtosecond optimal for critical stress-sensitive parts
- Electronics: Femtosecond required for sub-10μm features
For Production Applications Balancing Quality and Efficiency:
- Automotive tooling: Picosecond optimal for PCD and CBN tool manufacturing
- Industrial cutting tools: Picosecond provides best cost-performance ratio
- Precision molds: Picosecond suitable for most texturing applications
For Cost-Sensitive Applications with Moderate Precision Requirements:
- Rough machining: Nanosecond adequate with proper thermal management
- Non-critical components: Nanosecond cost-effective for basic processing
- Prototype development: Nanosecond suitable for concept validation
Future Investment Strategy
The continued evolution of ultrafast laser technology promises even greater capabilities and cost-effectiveness. Key considerations for strategic investment include:
- Scalability: Systems capable of accommodating future process requirements
- Flexibility: Multi-pulse duration capability for diverse applications
- Integration: Industry 4.0 compatibility for smart manufacturing
- Support: Comprehensive service and training infrastructure
Conclusion: Optimizing Laser Processing for Manufacturing Excellence
The selection between femtosecond, picosecond, and nanosecond laser processing fundamentally depends on balancing precision requirements, processing efficiency, and economic considerations. Performance data from real-world applications consistently demonstrates that shorter pulse durations provide superior precision and surface quality, while longer pulse durations offer higher processing rates and lower initial investment costs.
Implementation success depends on comprehensive understanding of material properties, application requirements, and total cost of ownership considerations. OPMT’s extensive experience in laser manufacturing solutions provides the technical expertise and proven track record necessary for successful ultrafast laser processing implementation across diverse industrial applications.
The continued evolution of ultrafast laser technology, combined with Industry 4.0 integration capabilities, positions laser processing as the preferred method for precision manufacturing. Strategic investment in appropriate pulse duration selection, supported by comprehensive training and technical support, ensures manufacturing competitiveness in precision industries while contributing to sustainable manufacturing practices.
For manufacturers evaluating ultrafast laser processing solutions, OPMT’s industry solutions provide comprehensive guidance for optimal technology selection and implementation success.
Disclaimer
This content is compiled by OPMT Laser based on publicly available information for reference only; mentions of third-party brands and products are for objective comparison and do not imply any commercial association or endorsement.