Laboratory-grown diamonds have revolutionized industrial applications by providing exceptional material properties while addressing critical environmental and ethical concerns associated with traditional mining operations. Through advanced laser processing technologies, these synthetic diamonds deliver superior technical performance in high-precision manufacturing, cutting tools, optical components, and thermal management solutions across multiple industries.
Production Technologies for Lab-Grown Diamonds
Lab-grown diamonds are manufactured through two primary methods, each offering specific advantages for industrial applications:
High Pressure High Temperature (HPHT) synthesis replicates natural diamond formation conditions by subjecting carbon to extreme pressure (5-6 GPa) and temperatures exceeding 1500°C. This method excels in producing industrial-grade diamonds particularly suitable for cutting tools and abrasive applications.
Chemical Vapor Deposition (CVD) operates at lower pressures (approximately 30-300 Torr) with temperatures of 700-1200°C, decomposing carbon-containing gases (typically methane) to precipitate carbon atoms onto a substrate, forming diamond crystal structures. CVD enables larger, high-purity crystals ideal for electronics and optical applications.
Both processes require sophisticated precision finishing with specialized laser processing equipment like the DiaCUT L315V CVD Laser Diamond Surface Grinding Machine to achieve the exacting specifications required for industrial components.
Environmental Advantages
Reduced Environmental Impact
The environmental benefits of lab-grown diamonds compared to traditional mining are substantial and quantifiable:
Environmental Factor | Traditional Mining | Lab-Grown Production | Advantage |
---|---|---|---|
Chemical usage | Strong acids required | None required | Elimination of hazardous chemicals |
Waste production | Chemical pollution | Dust filtration systems | Significant reduction in harmful waste |
Resource consumption | High water usage, consumable tools | No water cooling, no consumables | Resource conservation |
Land disturbance | Extensive mining operations | No land disturbance | Habitat preservation |
Precision/material waste | Variable accuracy, higher scrap rate | Consistent 0.003mm accuracy | Less material waste |
Modern diamond manufacturing facilities are increasingly adopting renewable energy systems to minimize their environmental footprint, aligning with growing consumer and industrial demand for sustainable production methods. OPMT’s laser systems utilize advanced dust-pelletizing systems that capture particulate matter without chemical waste generation, eliminating hazardous chemical consumables and simplifying regulatory compliance.
Precision Manufacturing Benefits
The exceptional precision of laser processing (consistent accuracy of 0.003mm) significantly reduces material waste through lower rejection rates and optimized material usage. This precision is particularly valuable when processing expensive diamond materials.
Traditional chemical texturing methods produce side etching and edge effects, resulting in poor 3D effects and rough textures. These processes typically involve harsh chemicals that require specialized disposal protocols and create workplace hazards. In contrast, OPMT Laser’s systems eliminate these concerns while delivering superior results.
Ethical Supply Chain Considerations
Laboratory-grown diamonds offer significant ethical advantages through transparent and controlled production environments. Unlike mined diamonds, which have sometimes been associated with conflict zones and problematic labor practices, lab-created diamonds are manufactured under controlled conditions with verifiable ethical labor standards.
The manufacturing transparency allows industrial users to incorporate lab-grown diamond components into products requiring detailed supply chain verification. This is increasingly important as industrial end-users face growing pressure to satisfy sustainability reporting requirements and ethical procurement guidelines.
Technical Applications in Industrial Settings
Precision Cutting and Machining Applications
Lab-grown diamonds enable exceptional performance in cutting applications through integration with advanced laser CNC systems. OPMT’s Light 5X 40V and Light 5X 60V laser machining centers achieve positioning accuracy of 0.005mm through linear motor drives, complementing diamond tooling capabilities for exceptional precision across diverse material types.
These systems are specifically designed for processing polycrystalline diamond (PCD), cubic boron nitride (CBN), hard alloys, ceramics, and other superhard materials. The integration of diamond components with precision laser systems creates manufacturing capabilities that combine:
- Extreme hardness (10 on Mohs scale)
- Superior wear resistance
- Exceptional thermal conductivity
- Optical transparency across broad wavelength ranges
Tool wear mechanisms differ significantly between lab-grown diamond tools and conventional alternatives, extending replacement intervals and reducing production interruptions. The thermal stability allows higher cutting speeds without cooling fluid in many applications, supporting dry machining processes that eliminate problematic coolant waste streams.
Thermal Management Solutions
The exceptional thermal conductivity of lab-grown diamonds (significantly outperforming conventional materials like copper and aluminum) enables breakthrough solutions for thermal management challenges in high-power laser systems and electronic applications. This property allows compact design of high-power laser systems without sacrificing performance or reliability.
Advanced metallization techniques create reliable thermal interfaces between diamond components and conventional system materials, minimizing thermal barriers and maximizing performance benefits throughout the entire thermal pathway.
Optical Components for Laser Systems
Lab-grown diamonds provide exceptional optical properties for high-performance laser systems, transmitting wavelengths from deep ultraviolet through to far infrared. This broad transmission range allows a single diamond window to replace multiple specialized components in complex laser systems, simplifying optical design and reducing potential failure points.
The exceptional hardness of diamond optical components provides unmatched resistance to environmental damage, maintaining optical performance in harsh industrial environments where conventional optics would require frequent replacement.
OPMT Laser’s Diamond Processing Technology
OPMT Laser offers specialized equipment for lab-grown diamond processing:
DiaCUT L315V CVD Laser Diamond Surface Grinding Machine
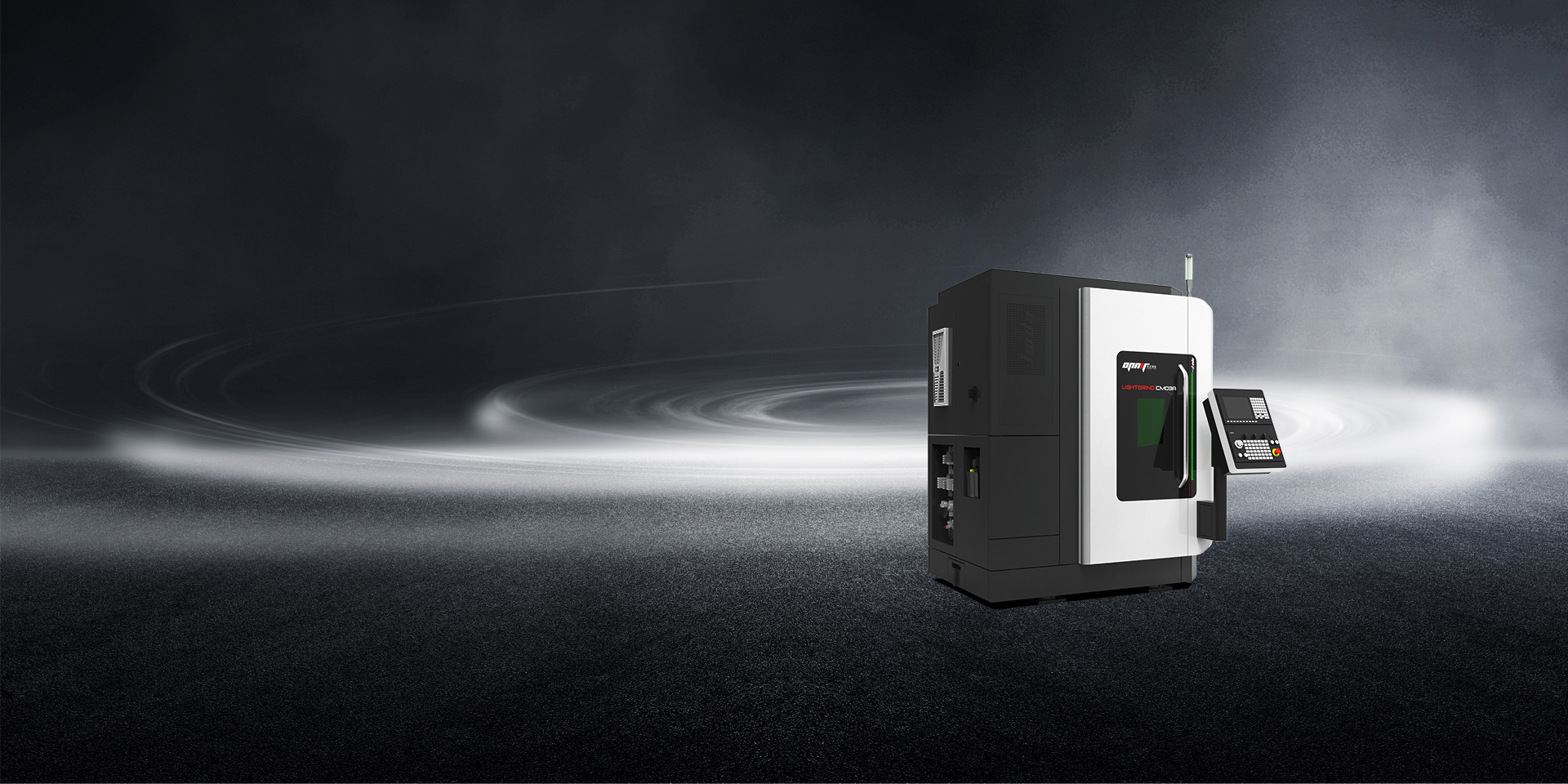
This system is specifically designed for CVD diamond processing with features including:
- Wavelength: 532nm for optimal diamond processing
- Positioning accuracy: 0.01mm
- Repeat positioning accuracy: 0.002mm
- Granite construction for vibration absorption and thermal stability
Light 5X Series Laser Machining Centers

These vertical 5-axis laser machining centers are ideal for complex diamond component manufacturing:
- Linear motor drives for fast dynamic response
- Closed-loop grating scale detection for high positioning accuracy
- Linear rolling guide rails for low friction coefficient and fast response
- Marble machine bed construction for stability, rigidity and thermal stability
- Capable of processing workpieces with large-curvature surfaces and complex contours
Compared to conventional EDM (Electrical Discharge Machining) methods, OPMT’s laser processing technology offers:
- 53% lower operational costs
- 3x faster production rates
- Zero chemical waste
- Consistent accuracy of 0.003mm
- Elimination of wire skipping issues when machining polycrystalline diamonds with inconsistent conductivity patterns
Economic and Implementation Considerations
Despite higher initial acquisition costs, lab-grown diamond components processed with laser technology deliver compelling total cost of ownership advantages in industrial applications when analyzed across complete operational lifecycles. The extended service life of these components reduces replacement frequency and associated production interruptions.
The smaller floor space requirements for laser processing equipment (6m² vs. 10m² for EDM) and lower electricity consumption (2.5 kW/h vs. 4.5 kW/h) further contribute to operational cost savings.
Processing Capability Example
For specific applications like saw blade tooth processing, OPMT’s laser CNC machine demonstrates significant efficiency advantages:
- Processing time for a trapezoidal flat tooth saw blade (diameter 500mm with 120 teeth): 8 hours vs. 24 hours with conventional EDM methods
- One-clamping operation completes roughing and finishing of the top and side of the saw blade, reducing cumulative process error
Future Outlook and Industry Transformation
The accelerating adoption of lab-grown diamonds in industrial applications is driving significant transformation throughout manufacturing value chains while delivering substantial sustainability benefits. As production technologies mature and scale economies drive continued cost reductions, the range of economically viable applications continues expanding.
Future innovations in diamond manufacturing technology, material integration techniques, and novel applications promise to further accelerate industrial adoption. The convergence of exceptional technical performance, compelling sustainability benefits, and improving economic value positions lab-grown diamonds to fundamentally transform industrial capabilities while simultaneously supporting broader environmental and ethical responsibility objectives.
Conclusion
Lab-grown diamonds represent a transformative technology for industrial applications, delivering exceptional technical performance while simultaneously addressing critical environmental and ethical concerns. Their unique combination of extreme hardness, unmatched thermal conductivity, and optical versatility enables performance capabilities unattainable with conventional materials, particularly in demanding laser system applications and precision manufacturing operations.
OPMT Laser’s specialized equipment for lab-grown diamond processing delivers the precision, efficiency, and environmental benefits that modern industrial manufacturers require. By eliminating chemical waste, reducing resource consumption, and achieving exceptional accuracy, these systems represent the future of sustainable high-precision manufacturing.
For more information on OPMT Laser’s diamond processing solutions, visit OPMT Laser’s Product Categories or explore our advanced laser solutions for precision manufacturing.
Disclaimer
This content is compiled by OPMT Laser based on publicly available information for reference only; mentions of third-party brands and products are for objective comparison and do not imply any commercial association or endorsement.